Sheet components made of titanium and its alloys mostly concentrate in aircraft areas where high strength-to-weight ratio combined with excellent corrosion resistance and strength at elevated temperatures requests must be met. The pylons, the nacelles or the engine itself are sub-assemblies where many of these components are found. Examples include after pylon fairings, fan blades, exhaust ducts or air collectors. Additionally, growing use of composite structure is making the content of titanium sheet components increase in the airframe due to titanium galvanic compatibility with the carbon fibres which is not fully guaranteed by corrosion protective coating of aluminium. Moreover, titanium can also be found in areas where specific requests make it the best choice. Such is the case, for instance, of the cabin area where the crown panel must show high impact resistance to withstand the damage incurred during bird strikes. Thus, titanium made sheet components seem likely to progressively increase in order to contribute to the weight reduction requested to decrease fuel consumption and consequent CO2, NOx and noise emissions which penalize the environmental impact of aviation.
However, forming technologies being used today by the aircraft industry to shape titanium (e.g. cold/hot stamping, SPF, hydroforming) make use of specific tooling which feature high costs and long lead times. Modifications in the tooling due to iteration between the design and industrialization phases and more and more frequent design evolutions also penalize costs and lead times.
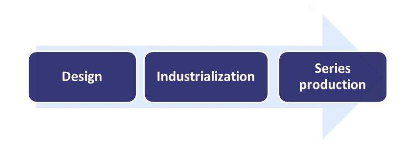
The INMA project aimed to lead to cost reduction and increased flexibility when shaping titanium, and other other difficult-to-deform materials, by introducing the asymmetric the incremental sheet forming technology (AISF) into the production chain.
AISF is a technology which features the potential to produce complex sheet metal parts without dedicated tooling. Thus, the development costs are reduced and agility and flexibility are gained during the design phase for prototyping or the production of spare parts and very low volume series.
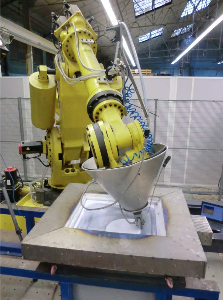
Asymmetric incremental forming robotic cell
In order to make use of the AISF technology to shape titanium, as well as other difficult to deform materials (e.g. Ni-base alloys) the following objectives were defined:
- Generate process data from experimental forming trials for the alloys of interest
- Implement and validate FE models that provide process simulation capabilities
- Perform material testing and analysis to generate a data base of the deformed material conditions
- Make use of knowledge-based (KB) techniques to generate systematic correction of the part geometric deviations
- Implement hot forming means and methods to deform relevant alloys (i.e. ti 6Al-4V)