Short summary
In the aircraft, there are high costs and long lead times associated to the production of sheet metal parts made of titanium and other difficult-to-deform materials such as after pylon fairings, fan blades, exhaust ducts or air collectors because the forming technologies used today (cold/hot stamping, SPF) are based on dedicated tooling.
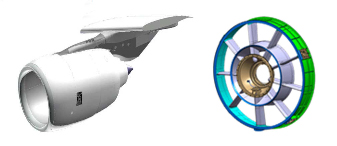
The INMA project aimed to decrease production costs and to gain flexibility when manufacturing sheet metal parts made of titanium and other difficult-to-deform materials by introducing the asymmetric incremental sheet forming technology (AISF) into the production chain.
The AISF technology shows the potential to produce complex sheet metal parts without dedicated tooling. Thus, the development costs can be reduced and agility and flexibility be gained during the design phase for prototyping or the production of spare parts and low volume series.
The project contents were oriented to the deployment of an AISF technology for titanium and other difficult-to-deform materials and considered: generation of experimental process data, acquisition of process numerical simulation capabilities, characterization through material testing and analysis of the deformed material properties, development of a knowledge-based (KB) tool path correction utility to compensate the part geometric deviation and implementation of hot forming for materials of interest, namely Ti 6Al-4V. Relevant foreground was generated in all these fields and allowed fabricating an Inconel 718 strut half and two generic shapes made of Ti 6Al-4V showing typical design features of pylon fairings.
The assessment of these parts reported promising results about the attainable quality of parts, even in terms of the geometric accuracy, representing a significant step forward towards the future industrialization of technology.
The integration of the AISF technology in the aeronautic production will not only bring cost reduction and increased flexibility through specific tooling avoidance but also other benefits such as a decreased consumption of lubricants and energy or new job opportunities for researchers. Relevant industrial participation in the project makes very likely the rapid orientation of the generated results towards its acceptance, approval and final exploitation.
The INMA project has received funding from the European Union‘s Seventh Framework Programme for research, technological development and demonstration under grant agreement No 266208.
Project's final summary report available here.
Impact
Main benefit expected from introducing the technology in the production chain will come from the avoidance or decreased use of specific tooling which will have a strong impact on the component final cost and its associated lead time from the design office to serial production. In particular, by producing prototype parts using the AISF process interaction between the design and industrialization phases does not make use of specific tooling. In the case of the production of spare parts or low volume series the impact is much higher.
There are additional benefits that can also be expected:
- Decreased consumption of expensive (and usually very pollutant) lubricants since roller tools lead to lower friction between the sheet and the tool.
- Higher buy-to-fly ratios compared to SPF resulting from a better control of thickness.
- Decreased energy consumption of hot forming operations compared to SPF since the working temperature is lower.
- Reduced stocks of tooling derived from their avoidance to fabricate prototypes, spare/repair parts and low volume series.
The new technology will also contribute to bring new job opportunities for researchers and to strengthen the leadership position of the European aircraft industry.
Consortium partners
TECNALIA
EADS Innovation Works
Industrias Puigjaner S.A.
Vyzkumny a zkusebni letecky ustav (Aeronautical Research and Test Institute) (VZLU)
University of Patras / LTSM
TWI
Institut für Bildsame Formgebung der RWTH Aachen - (RWTH-IBF)
Wytwornia Sprzetu Komunikacyjnego PzL–Rzeszow (WSKRZ)
The University of Liverpool
The European Aeronautics Science Network Association
AIRBUS Operations S.A.S.